Almost every advancement in tool materials brings a revolution to the machining industry. The alternate development of machine tools and tool materials has become a historical law for the continuous development of cutting technology.The development history of metal cutting, in a sense, can be attributed to the development history of tool materials.
In order to complete the cutting, in addition to requiring the tool to have a reasonable angle and proper structure, the material of the tool is an important basis for cutting.
During the cutting process, the cutting tool works under strong cutting force and high temperature, and at the same time produces severe friction with the chip and the workpiece surface, so the working conditions are extremely harsh. In order to make the cutting tool have good cutting ability, suitable materials must be selected. The cutting tool material has a great influence on the processing quality, productivity and processing cost.
The properties that the tool material should have:
1.High hardness and wear resistance
2.Sufficient strength and toughness
3.High heat resistance
4.Good thermal physical properties and heat -resistant impact performance
5.Good craftsmanship
6.Cost -effective
Some of the above properties are contradictory (for example, the higher the hardness, the better the wear resistance, the poorer the toughness and resistance to breakage, the better the heat resistance, the poorer the toughness).
In actual work, the most suitable tool material should be selected according to the specific cutting objects and conditions.
Common tool materials.
Classification of tool materials:
Tool steel: carbon tool steel, alloy tool steel, high-speed tool steel;
Cemented carbide: ordinary cemented carbide, fine-grained cemented carbide, micro-grained cemented carbide; there are tungsten-cobalt-based cemented carbide, tungsten-titanium-cobalt-based cemented carbide and tungsten-titanium-tantalum (niobium)-based cemented carbide.
Ceramics: oxide ceramics, nitride ceramics;
Super-hard materials: cubic boron nitride, diamond
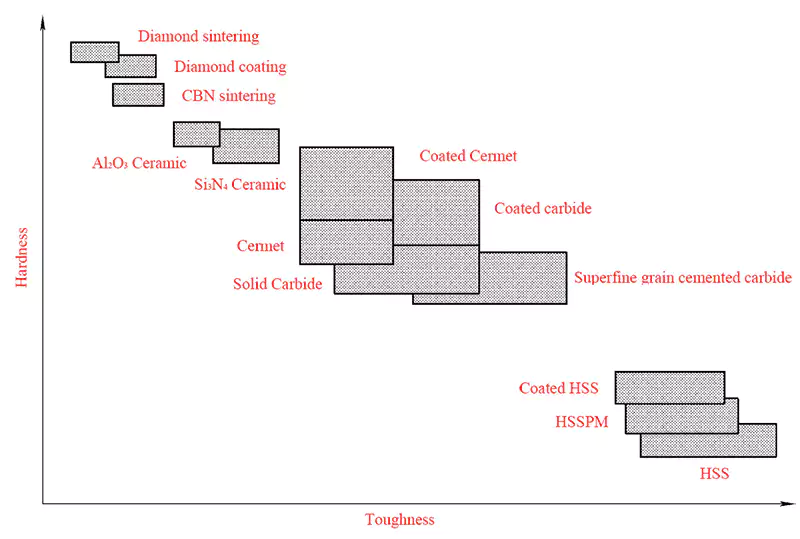
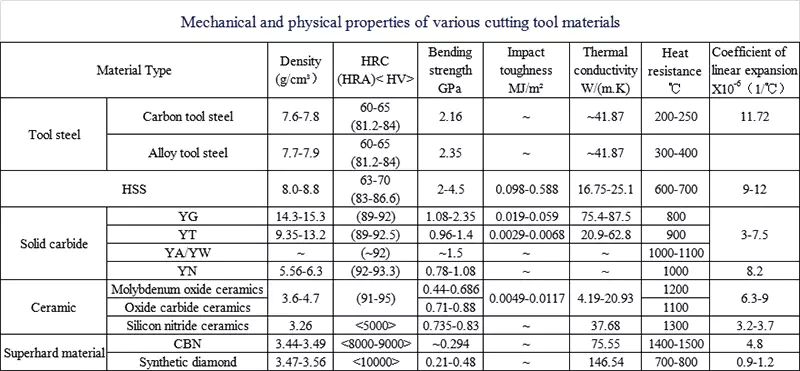
Common tool material–carbon tool steel
Alloy tool steel
Adding a certain amount of alloying elements such as chromium (Cr), tungsten (W), manganese (Mn) to carbon tool steel can improve the heat resistance, wear resistance and toughness of the material, and can also reduce the deformation during heat treatment. .
1. The main grades are: 9SiCr CrWMn
2. Main properties: The hardness after quenching can reach HRC61~65, the red hardness is 300℃~400℃, and the allowable cutting speed Vc=10~15m/min. Such as die, broach, hand reamer (finishing of holes), etc.
Common tool material – high speed steel
High speed steel
High-speed steel is a kind of high-alloy tool steel, which contains W, Mo, Cr, V and other alloying elements.
Features: After heat treatment, the hardness can reach 62~66HRC, the bending strength is about 3.3GPa, and it has high thermal stability, wear resistance and heat resistance. Cutting can still be performed when the cutting temperature is 500~650°C.
Application: Due to the small heat treatment deformation, the ability to be forged and easy to grind, it is especially suitable for the manufacture of tools with complex structures and blade shapes, such as forming turning tools, milling tools, drills, gear cutters, threading tools and broaches.
In order to improve the hardness and wear resistance of high-speed steel, the following measures are often used to improve its performance:
(1) Add new elements to high-speed steel;
(2) Eliminate the segregation of carbides and refine the grains by powder metallurgy.
Properties of high speed steel
1. Has high strength and toughness
2. Good wear resistance
3. The red hardness is 600℃
4. Allowable cutting speed Vc=25-30m/min
5. Good manufacturing process
6. You can get a sharp blade
7. Larger processing range: cast iron, non-ferrous metals, steel
Classification of high speed steel
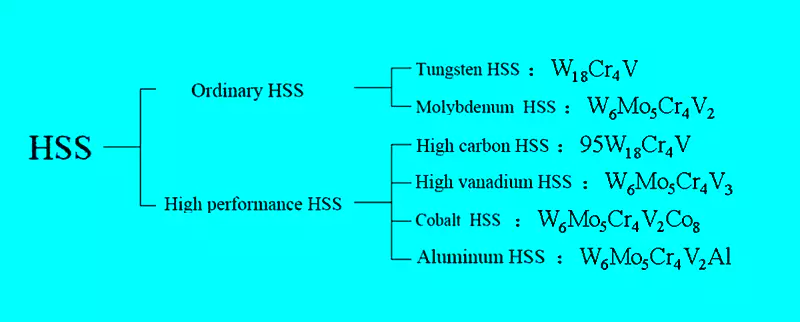
Powder metallurgy high speed steel
HSSPM is obtained by atomizing molten high-speed steel molten steel with high-pressure argon or pure nitrogen to obtain fine high-speed steel powder, and then hot forging and rolling.
Features: It effectively solves the problem of eutectic segregation of coarse carbides in ingots when generally smelting high-speed steel, and obtains a fine and uniform crystalline structure, so that it has good mechanical properties. Its strength and toughness are 2 times and 2.5~3 times that of smelting high-speed steel respectively; the grinding processability is good; the physical and mechanical properties are highly isotropic, and the quenching deformation is small; the wear resistance is increased by 20%~30%.
Suitable for manufacturing precision tools, large size (hob, gear shaper) tools, complex forming tools, broaches, etc.
Common tool material– solid carbide
Carbide
Cemented carbide is made of refractory metal carbides (such as WC, TiC) and metal binders (such as Co) by powder metallurgy.
Features: Cemented carbide has high hardness, wear resistance and heat resistance. The hardness can reach HRA 89~93, and it can also bear cutting at 800~1000℃, and its durability is dozens of times higher than that of high-speed steel. When the durability is the same, the cutting speed can be increased by 4 to 10 times. The strength and toughness are lower than those of high-speed steel, only 0.9~1.5 GPa (90~150 kgf/mm), and the craftsmanship is poor, and it cannot withstand large vibration and shock loads during cutting. Suitable for manufacturing high-speed cutting tools. Most turning tools, end mills, etc. are made of carbide;
Main performance
- Hardness 74-81.5HRC, red hardness 800℃–1000℃, excellent wear resistance
- The allowable cutting speed Vc=100m/min or more, the maximum does not exceed 200m/min
- It is brittle and should avoid shock and vibration. Chipping is easy to occur, so pay attention to the processing conditions
- The processing range is wide. Brittle materials, steel, non-ferrous metals can be processed
The hard alloy is made of metal carbides with high heat resistance and high wear resistance (tungsten carbide WC, titanium carbide TiC, tantalum carbide TaC, niobium carbide NbC, etc.) and metal binders (cobalt, nickel, molybdenum, etc.) Powder metallurgy products sintered at high temperature. Its hardness is HRA89~93, it can withstand high temperature of 850~1000℃, and has good wear resistance. The allowed cutting speed can reach 100~300m/min, and it can process various materials including hardened steel. widely used. However, hard alchemy has low bending strength, poor impact toughness, unsharp cutting edge, difficult machining, and is not easy to make integral tools with complex shapes, so it cannot completely replace high-speed steel at present. Commonly used hard alloys are tungsten cobalt (YG type), tungsten cobalt titanium type (YT type) and general cemented carbide (YW type). The corresponding ISO standards are: K, P, M types
Examples of the representation method of cemented carbide grades are as follows:
Y: the first letter of the hard pinyin
G6: G6 – tungsten-cobalt alloys and cobalt content.
T15 – tungsten-cobalt-titanium alloy and TiC content.
W – tungsten cobalt titanium tantalum alloy.
N – tungsten titanium nickel molybdenum alloy
X: Additional letters indicate respectively
X – fine grain
C – coarse grain
N——Add niobium element
A——Add tantalum element
Tungsten Cobalt Cemented Carbide (YG)
Tungsten Cobalt Titanium Cemented Carbide (YT)
Add rare metal carbide (YA/YW)
Titanium carbide based cemented carbide (YN)
1. Tungsten-cobalt-based cemented carbide (YG): (K-type) (the number indicates the Co content in the alloy)
Commonly used grades: YG6, YG8, YG3X, YG6X, where the number is the percentage of cobalt content, X represents fine grain
YG3 (finishing) YG6 (semi-finishing) YG8 (roughing)
The content of Co increases, the toughness increases, the strength increases, the HRC decreases, and the wear resistance decreases.
The content of Co decreases, the toughness decreases, the strength decreases, the HRC increases, the wear resistance increases, and the brittleness increases
Composed of WC and Co. The hardness is HRA89~91.5, and the bending strength is 1.1~1.5 GPa (110~150 kgf/mm2). There are coarse grains, medium grains, fine grains, and ultrafine grains. Generally, it has a medium-grain structure,
Features: Fine-grained cemented carbide has higher hardness and wear resistance than medium-grained cemented carbides with the same cobalt content, but lower flexural strength and toughness.
Application: It is more suitable for machining hard and brittle cast iron, non-ferrous metals and non-metallic materials with short chips. High cobalt content is used for roughing.
2. Tungsten Cobalt Titanium Cemented Carbide (YT): (P Type) Hard Phase (WC+TiC) + Binder Phase (Co)
Commonly used grades: YT5, YT14, YT15, YT30, etc., the number is the percentage of TiC content, and the corresponding cobalt content is 10%, 8%, 6%, 4%, TiC content increases, Co content decreases,
YT5 (finishing) YT14/YT15 (semi-finishing) YT30 (roughing)
TiC content increases, hardness increases, wear resistance increases, brittleness increases, and toughness decreases
TiC content decreases, hardness decreases, wear resistance decreases, brittleness decreases, and toughness increases
In addition to WC, it also contains 5% to 30% TiC. The hardness and wear resistance are increased, but the flexural strength, especially the impact toughness, is significantly reduced. Its hardness is HRA 89.15~92.5, and its flexural strength is 0.9~1.4 GPa (90~140 kgf/mm2).
Features: This kind of alloy has high hardness and wear resistance, especially high heat resistance, good anti-bonding diffusion ability and anti-oxidation ability; but the bending strength, grindability and thermal conductivity decrease, and the low temperature brittleness is large. , poor toughness.
Application: suitable for processing steel. Not suitable for machining stainless steel and titanium alloys. Due to the affinity between the titanium element in YT and the titanium element in the workpiece, the phenomenon of severe tool sticking will occur, and the tool wear will be aggravated in the case of high temperature cutting and high friction coefficient.
It is mainly used for processing steel and non-ferrous metals, and is generally not used for processing Ti-containing materials, such as 1Cr15Ni9Ti. The affinity between Ti and Ti is large, which makes the tool wear faster.
- Add rare metal cemented carbide (M class)
Tungsten-tantalum (niobium) cobalt-based cemented carbide (YA) and tungsten-tantalum (niobium)-cobalt-based cemented carbide (YW) are the addition of TaC (NbC) to tungsten-cobalt-titanium-based cemented carbide (YT), which can improve the Its flexural strength, fatigue strength and impact toughness can improve the high temperature hardness and high temperature strength of carbide, and improve the oxidation resistance and wear resistance. Commonly used grades are YW1 and YW2.
Application: It can be used for machining cast iron and non-ferrous metals, as well as steel. Therefore, it is also known as general-purpose cemented carbide. When the cobalt content is high, the strength and impact toughness are high, which can be used for roughing and interrupted cutting; the low cobalt content has good wear resistance and heat resistance, and is used for semi-finishing and finishing. Therefore, they often become general-purpose cemented carbides, and they are mainly used for machining difficult-to-machine materials.
- Titanium carbide based cemented carbide (YN)
TiC-Ni-Mo alloy with TiC as main component and Ni and Mo as binder
Features: high hardness, high wear resistance, high heat resistance and oxidation resistance, good chemical stability, strong anti-bonding ability, high tool durability.
Application: Can machine steel and cast iron, mainly used for finishing and semi-finishing of continuous surfaces of steel

Coated cutter
Coated tools are made by coating a thin layer of refractory metal compounds with high wear resistance on hard alloy matrix or high speed steel tool matrix with good toughness.
Coated cemented carbide is generally deposited by chemical vapor deposition at about 1000℃. Coated high-speed steel tools generally adopt physical vapor deposition, and the deposition temperature is about 500℃.
Commonly used coating materials are TiC, tin, Al2O3, etc.
Coating thickness: cemented carbide is 4~5 μm, and the surface hardness can reach HV2500~4200; The high-speed steel is 2 μm, and the surface hardness can reach HRC 80.
Coating tool features:
Advantages: high wear resistance and crescent wear resistance; Low friction coefficient can reduce cutting force and cutting temperature, and improve tool durability (the durability of cemented carbide tools is increased by 1-3 times, and that of high-speed steel tools is increased by 2-10 times).
Disadvantages: Poor sharpness, toughness, anti-peeling, anti-chipping and high cost.
1. TiC coating: it has high hardness, good wear resistance and oxidation resistance, and can produce titanium oxide film during cutting, thus reducing friction and tool wear.
2. TiN coating: It can produce oxide film at high temperature, has small friction coefficient with iron-based materials, good anti-bonding performance, and can effectively reduce cutting temperature.
3. TiC—TiN composite coating: the first layer is coated with TiC, which is stuck to the tool base and is not easy to fall off. The second layer is coated with TiN to reduce the friction between the surface layer and the workpiece.
4. TiC-Al203 composite coating: the first layer is coated with TiC, which is stuck to the tool base and is not easy to fall off. The second coating of Al203 can make the tool surface have good chemical stability and oxidation resistance.
At present, single-coated blades are rarely used, and TiC-TiN composite coating or TiC-Al2O3-TiN triple composite coating is mostly used.
Other tool materials
I. Ceramics
Ceramic: A kind of cutting tool material made of alumina (Al2O3) or silicon nitride (Si3N4) as matrix and a small amount of metal, which is sintered at high temperature.
characteristic
Advantages: high hardness, good wear resistance, high temperature resistance, good chemical stability and oxidation resistance, low affinity with metal, strong anti-adhesion and anti-diffusion ability;
Disadvantages: high brittleness, low bending strength, poor impact toughness and easy edge collapse, so the application range is limited;
Application: It can be used for turning and milling of steel and cast iron parts. The finishing stage of high-speed cutting.
2.Diamond
Diamond: the allotrope of carbon, which is converted from graphite at high temperature and high pressure, is the hardest substance artificially produced at present.
Characteristic
Advantages: High hardness, good wear resistance, and tool durability can be improved several times to hundreds of times compared with cemented carbide. The cutting edge is sharp, the friction coefficient of the blade surface is small, it is not easy to produce sticking or chip accumulation, and the phenomenon of cold and hard machining is less, so it is very suitable for precision machining.
Disadvantages: poor thermal stability, cutting temperature should not exceed 700~800℃; Low strength, high brittleness, sensitive to vibration, only suitable for micro-cutting, and strong chemical affinity with iron, so it can’t be used for processing steel materials.
Application: At present, it is mainly used for grinding tools and abrasives, and can be used for processing high-hardness and high-wear materials such as cemented carbide, ceramics, high-silicon aluminum alloy and wear-resistant plastics, and materials with hardness of 65~70HRC such as cemented carbide and ceramics. It can also be used to process non-metallic materials with high hardness, such as stone, compressed wood, glass, etc. It can also be used to process non-ferrous metals, such as Al-Si alloy materials and composite materials that are difficult to process.
When used as tool material, it is mostly used for fine turning or boring non-ferrous metals and nonmetallic materials at high speed. When processing aluminum alloy and copper alloy, the cutting speed can reach 800~3800 m/min.
Cubic boron nitride (CBN)
Cubic boron nitride (CBN) is a new tool material synthesized artificially. It is converted from hexagonal boron nitride by adding catalyst at high temperature and high pressure.
Features: It is a superhard material (HV8000~9000) with extremely high hardness but extremely poor toughness, high hardness and wear resistance, good thermal stability, large chemical inertia, difficult chemical reaction with iron-based metals at 1300℃, good thermal conductivity and low friction coefficient.
Application: Therefore, it can be used for semi-finishing and finishing of various difficult-to-machine materials such as high-temperature alloy, chilled cast iron, hardened steel, etc., with high machining accuracy and low surface roughness, and can replace grinding. Cubic boron nitride is not only used in grinding tools, but also gradually used in turning, boring, milling and reaming.