With the development of high-speed cutting technology, great changes have taken place in high-speed cutting tool materials and tool manufacturing technology, and new materials, new coatings and new technologies are constantly emerging. However, at present, cutting tool technology is still a technical bottleneck that restricts the improvement of machining efficiency of difficult-to-machine materials such as titanium alloy. SZSUNLIT high-performance composite coating SZR milling cutter was born, which has good anti-sticking.
About titanium alloys
Titanium and titanium alloys play an important role in a country’s national defense, economy and scientific and technological development. They are called strategic metals in the 21st century, and are also called “the third generation metal”. Compared with common metals, titanium alloy has better strength, toughness, ductility, oxidation resistance and corrosion resistance, which makes titanium alloy widely used in high-tech fields such as aerospace, automobile and chemical industry. In addition, because of its good biocompatibility, titanium alloy has become the most suitable biomedical metal material, and has been successfully applied to artificial knee joint, femoral joint, dental implant, tooth root and denture metal bracket, etc.
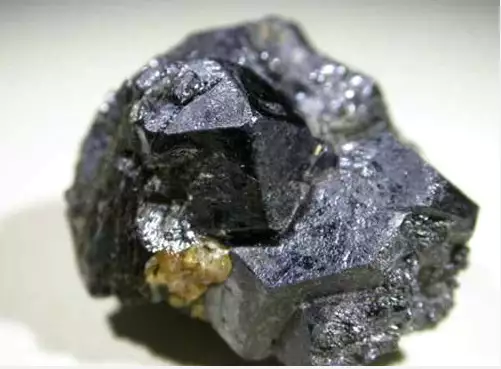
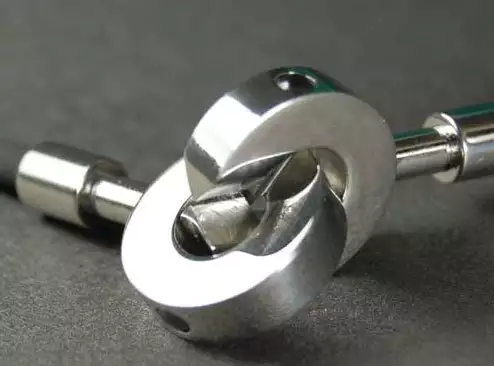
With the change of mainstream demand in China’s tool market, the lightweight policy and the development trend of the industry, titanium alloy has gradually become popular from military industry to aerospace, to 5G mobile phones, smart wear and other industries. Based on the comprehensive performance of titanium alloy, its application scope is broader. For many cutter manufacturers, it can be regarded as an opportunity and development policy.
Machining difficulties of titanium alloy
Stainless steel, titanium alloy and nickel-base superalloy are the three traditional difficult-to-machine materials, and titanium alloy is the key and difficult point. Its low thermal conductivity, severe work hardening, high affinity with cutting tools and small plastic deformation, and its cutting index is only 20% of that of easy-to-cut steel, which leads to the rapid failure of cutting tools and short tool life. For titanium alloy, under the condition of tool strength and machine tool power, the cutting temperature is the key factor affecting tool life, not the cutting force. Therefore, when processing titanium alloy, it is necessary to choose special tools to ensure efficiency, which greatly increases the processing cost. How to overcome titanium alloy cutting is always a headache for tool manufacturers.
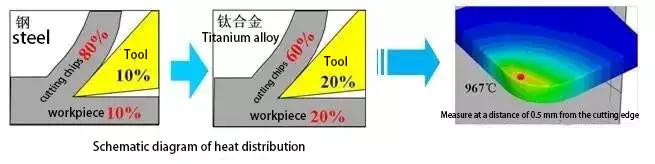
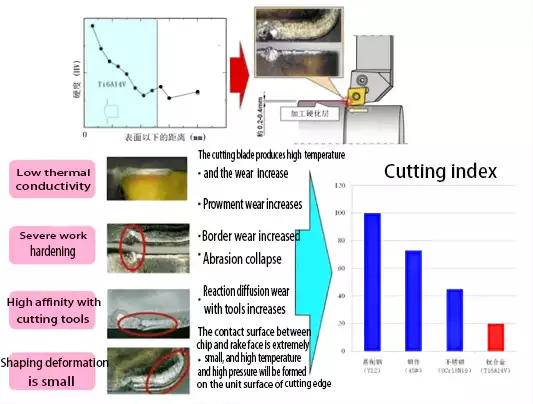
Solve the problem of titanium alloy cutting.
In view of the difficulty of cutting titanium alloy, the selected tool materials must meet the requirements of high hardness, high strength, large thermal conductivity, good chemical stability and red hardness. Because of the high price of superhard tools and ceramic tools, cemented carbide tools still occupy the main position in the titanium alloy cutting market. However, it is more effective and stable to optimize the performance of existing tools, such as using the surface treatment scheme-PVD coating. SZSUNLIT developed a functional coated SZR milling cutter suitable for high-speed cutting of titanium alloy.
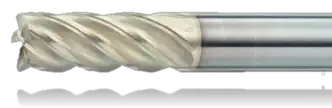
Coating introduction
In the future, 3C industry will consider using titanium alloy and aluminum alloy materials, and SZR is developed for processing these materials. It belongs to Ti-Si base with special elements added, and its multilayer compact structure can effectively prevent chemical diffusion. It has high hardness, wear resistance, oxidation resistance and anti-sticking performance, which greatly improves the comprehensive performance of the cutter and prolongs its service life.
Coating parameters

Application case
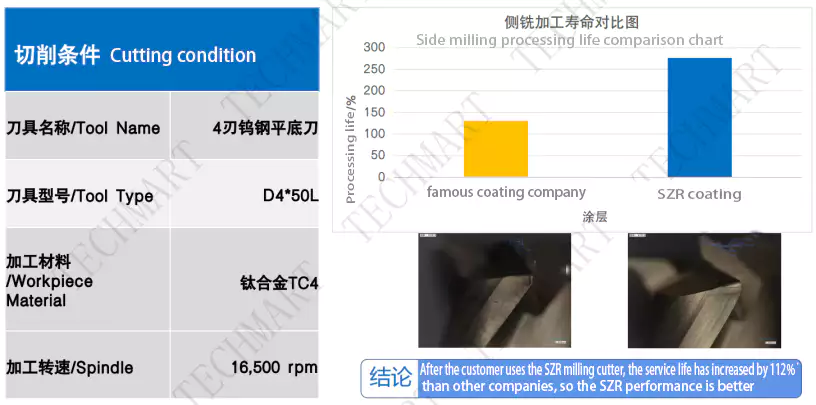
Use effect
Compared with other competitive coatings, the processing life of SZR is increased by 112%, and its performance is more outstanding and superior. The coating reduces the times of tool change due to wear, increases the production efficiency and improves the processing quality.